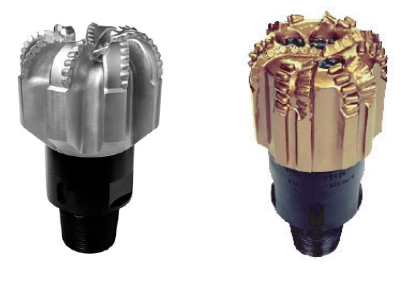
Unfortunately, the best bit to drill a given formation is selected by trial and error. The criterion used for selecting a bit is based on the drilling cost per unit interval (check also drilling cost per foot).
The cost-per-foot equation
The bit that would give the least drilling cost is the best bit for drilling a given formation.
The drilling cost per foot. C is,
The initial selection of bit type
The initial selection of bit type can be made based on formation drillability and abrasiveness.
- Drillability is a measure of how easily the formation is drilled, and it is inversely related to the compression strength of the rock.
- The abrasiveness of the formation is a measure of how rapidly the teeth of a milled tooth bit wear when drilling the formation.
- Normally, abrasiveness increases as the drillability decreases.
The drilling cost per foot is the final criterion that should be used for selecting a bit.
Rule Of Thumb
Some of the rules of thumb used for bit selection are:
- High-cost bits tend to be more applicable when the daily rig operation cost is high.
- Rolling cone bits are the most versatile bits and are a good initial choice.
- Diamond drag bits perform best in nonbrittle formations having a plastic mode of failure, especially in the bottom portion of a deep well, where the high cost of pipe tripping operations favors a long bit life, and a small hole size favors the simplicity of a drag bit design.
- PDC drag bits perform best in uniform sections of carbonates or evaporites that are not broken up with hard shale stringers or other brittle rock types.
- PDC drag bits should not be used in gummy formations, which strongly tend to stick to the bit cutters.
When using a rolling cone bit:
- Use the longest tooth suitable for the application.
- When the rate of tooth wear is much less than the rate of bearing wear, select a longer tooth size, a better bearing design, or apply more bit weight.
- When the rate of bearing wear is much less than the rate of tooth wear, select a shorter tooth size, a more economical bearing design, or apply less bit weight.