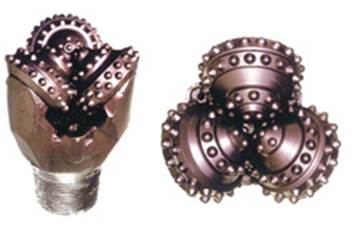
Criteria Of Roller Cone Bit Bit Performance
The performance of a Roller Cone bit may be judged on the following criteria:
- How much footage it drilled (ft).
- How fast it drilled (ROP).
- How much it cost to run (the capital cost of the bit plus the operating costs of running it in hole) per foot of hole drilled .
Since the aim of bit selection is to achieve the lowest cost per foot of hole drilled the best method of assessing the bits’ performance is the last of the above. This method is applied by calculating the cost per foot ratio, using the following equation:
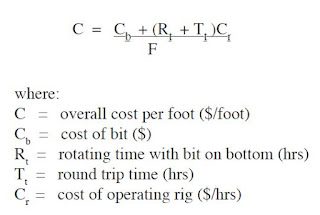
This equation relates the cost per foot of the bit run to the cost of the bit, the rate of penetration and the length of the bit run. It can be used for:
- Post drilling analysis to compare one bit run with another in a similar well.
- Real-time analysis to decide when to pull the bit. The bit should be pulled theoretically when the cost per foot is at its minimum.
Since penetration rate is one of the most significant factors in the assessment of bit performance this will be studied in greater depth.
In addition to correct bit selection penetration rate is a function of many parameters:
Weight on Bit
A certain minimum WOB is required to overcome the compressibility of the formation. It has been found experimentally that once this threshold is exceeded, the penetration rate increases linearly with WOB.
There are however certain limitations to the WOB which can be applied:
A- Hydraulic horsepower (HHP)
If the HHP at the bit is not sufficient to ensure good bit cleaning the ROP is reduced
either by:
- bit balling where the grooves between the teeth of the bit are clogged by formation cuttings (occurs mostly with soft formation bits), or
- bottom hole balling where the hole gets clogged up with fine particles (occurs mostly with the grinding action of hard formation bits).
If this situation occurs no increase in Roller cone bit performance ROP results from an increase in WOB unless the hydraulic horsepower (HHP) generated by the fluid flowing through the bit is improved. The HHP at the bit is given by:
To increase HHP, therefore, requires an increase in Pb (smaller nozzles) or Q (faster pump speed or larger liners). This may mean a radical change to other drilling factors (e.g. annular velocity) which may not be beneficial.
Hole cleaning may be improved by using extended nozzles to bring the fluid stream nearer to the bottom of the hole. Bit balling can be alleviated by using a fourth nozzle at the centre of the bit.
B. Type of formation
WOB is often limited in soft formations, where the excessive weight will only bury the teeth into the rock and cause increased torque, with no increase in ROP.
C. Hole deviation
In some areas, WOB will produce bending in the drill string, leading to a crooked hole. The drill string should be properly stabilized to prevent this from happening.
D. Bearing life
The greater the load on the bearings the shorter their operational life. Optimizing ROP will depend on a compromise between WOB and bearing wear.
E. Tooth life
In hard formations, with high compressive strength, excessive WOB will cause the teeth to break. This will become evident when the bit is retrieved. Broken teeth is, for example, a clear sign that a bit with shorter, more closely packed teeth or inserts is required.
Rotary Speed (RPM)
The Roller cone bit performance ROP will also be affected by the rotary speed of the bit and an optimum speed must be determined. The RPM influences the ROP because the teeth must have time to penetrate and sweep the cuttings into the hole. The figure below shows how ROP varies with RPM for different formations.
The non-linearity in hard formations is due to the time required to break down rocks of higher compressive strength. Experience plays a large part in selecting the correct rotary speed in any given situation.
The RPM applied to a bit will be a function of :
A. Type of bit
In general lower RPMs are used for insert bits than for milled tooth bits. This is to allow the inserts more time to penetrate the formation. The insert crushes a wedge of rock and then forms a crack that loosens the fragment of rock.
B. Type of formation
Harder formations are less easily penetrated and so require low RPM. A high RPM may cause damage to the bit or the drill string.
Mud Properties & Roller Cone Bit Performance
In order to prevent an influx of formation fluids into the wellbore the hydrostatic mud pressure must be slightly greater than the formation (pore) pressure. This overbalance, or positive pressure differential, forces the liquid portion of the mud (filtrate) into the formation, leaving the solids to form a filter cake on the wall of the borehole. In porous formations this filter cake prevents any further entry of mud into the formation. This overbalance and filter cake also exist at the bottom of the hole where it affects the removal of cuttings.
When a tooth penetrates the surface of the rock the compressive strength of the rock is exceeded and cracks develop, which loosen small fragments or chips from the formation. Between successive teeth, the filter cake covers up the cracks and prevents mud pressure from being exerted below the chip.
The differential pressure on the chip tends to keep the chip against the formation. This is known as the static chip hold-down effect, and leads to lower penetration rates. The amount of plastering which occurs depends on mud properties. To reduce the hold-down effect:
- Reduce the positive differential pressure by lowering the mud weight (i.e. reduce the overbalance to the minimum acceptable level to prevent a kick).
- Reduce the solids content of the mud (both clay and drilled solids). Solids removal is essential to increase drilling efficiency.
In less porous formations the effect is not so significant since the filter cake is much thinner. However dynamic chip hold down may occur. This occurs because, when cracks form around the chip mud enters the cracks to equalize the pressure. In doing so, however, a pressure drop is created which tends to fix the chip against the bottom of the hole.
The longer the tooth penetration, the greater the hold-down pressure. Both static and dynamic hold-down effects cause bit balling and bottom hole balling. This can be prevented by ensuring correct mud properties (e.g. mud weight and solids content).