Friction Coefficient Definition
Drill String Friction Coefficient determines how much of the normal force is transformed into drag or torque and it is an important factor in calculating Torque And Drag in a wellbore.
Drill String Friction Coefficient can be calculated from actual drilling situations for a particular well geometry using a computer program with Drill String surface loads as input data. Input includes pickup weight, slack-off weight and torque readings, each of which can produce independent friction coefficient.
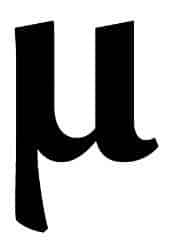
Agreement among the three coefficients from one well lends credibility to the model and also provides confidence in the friction coefficient for its use in the prediction of torque and drag in subsequent wells.
Calculation of Drill String Friction Coefficient during tripping out of hole:
By The Drill String Drag
The pickup load is read from the weight indicator. The reading from the weight indicator includes the weight of the oil and gas kelly and traveling equipment. In calculating drag forces, the tension at the top of the Drill Pipe below the kelly is required. Thus, it is necessary to subtract the weights of the traveling equipment and kelly from the weight indicator reading.
The tension at the top of the Drill Pipe, the Drill String and wellbore geometry data are entered in the computer program. The program calculates the tension required to pick up the Drill Pipe by using different coefficients of friction until the calculated tension is equal to the tension read by the indicator. The coefficient of friction at which the calculated tension is equal to the measured tension is the correct coefficient to use for that wellbore.
To ensure accurate results, the weight indicator must be calibrated to give accurate readings. Also accurate weights of the traveling equipment and kelly must be known.
By The Drill String Torque
Drill String Friction Coefficient can also be determined by measuring the torque while turning the drill string off the bottom. The torque must be in foot-pounds rather than amperes. The coefficient of friction where the measured torque is equal to the calculated torque is the correct coefficient for the wellbore.
Most rigs are not equipped with calibrated torque indicators and, therefore, it is recommended to determine friction coefficients by measuring tension.
Factors Affecting Drill String Friction Coefficient
- Mud Type
- Whether the hole is cased or open.
Typical ranges of Drill String friction coefficients :
Water-Based Mud | Oil Based Mud | |
Open Hole | 0.15-0.3 | 0.15 – 0.25 |
Cased Hole | 0.125 – 0.4 | 0.125-0.25 |
Torque And Drag arise not only from friction but also from:
- The effects of hole tortuosity,
- Cuttings accumulations,
- Swelling shale,
- Differential Sticking.
- Other mechanical impediments to Drill String movement.
Drag Coefficient
Thus, the friction coefficient in the Torque And Drag programs could be more accurately considered as a drag coefficient, Which is a composite coefficient that includes all factors affecting Torque And Drag. Furthermore, the drag coefficients for rotational movement, for axial movement, or for a combination of the two will often be different and may also vary with the direction of movement.
Finally, because these mechanical impediments to string movement frequently change with changing hole conditions, the friction coefficient will also fluctuate, particularly for axial movement.