Heavy weight drill pipe (HWDP) specs are important to understand as they are the entrance to the heavy-weight drill pipe design & selection. This article will discuss its definition, uses, and advantages. Furthermore, we provided specification tables that will greatly assist in selecting the drill string design. In addition to that, you can also download the spec sheets for any size of HWDP.
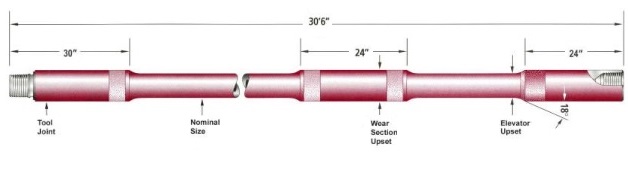
Heavy Weight Drill Pipe Definition
A heavy-wall drill pipe, normally called a hevi-wate drill pipe and abbreviated to HWDP, is an intermediate-weight drill string member. It consists of heavy-wall tubes with an upset in the middle, called the center wear pad, and special long tool joints, up to twice as long as normal drill pipe. As an example of the difference between standard drill pipe and heavy-wall drill pipe, Table 1 below compares the two using 5″ OD pipe.
As seen from the table, the external dimensions of HWDP are the same as drill pipe dimensions for easy handling. The extra weight comes from the additional wall thickness of the tube, the wear pad, and the longer tool joints. Because of its weight and construction, HWDP can be run in compression similarly to drill collars, subject to the normal constraints for buckling, i.e., except in large-diameter vertical holes.
In conclusion, a heavy-weight drill pipe normally has the same external dimensions as a regular one. In some types, the tool joints are longer; in others, an extra mock tool joint is located in the center of the joint, as shown in the drawing below.
HWDP Manufacturing Process
The figure below identifies the manufacturing process of the heavy-weight drill pipe.
Importance of HWDP in Drilling Operations
In the past, the two main components of the Drill String were the drill pipe and the drill collars. The transition Zone is the point where the relatively small OD and flexible Drill Pipe connect to the large stiff Drill Collars. Oilfield studies have shown that almost all of the drill string fatigue failures result from an accumulation of fatigue damage occurring when the drill pipe joints were run in the Transition Zone or were stressed above the endurance limit in crooked holes.
Downhole data has indicated that the large change in diameter at the transition zone caused accelerated fatigue damage due to the concentration of cyclic bending stress reversals in the bottom joints of the flexible Drill Pipe since the stiff Drill Collars bend very little from these stress reversals. So heavy weight drill pipe specs definition will be a drill pipes with higher thickness to withstand the stress concentration in the transition zone.
Features
Before discussing heavy-weight drill pipe specs, let’s understand its function. Heavy-weight drill pipe absorbs the stresses transferred from the stiff Drill Collars to the relatively flexible Drill Pipe. The major HWDP benefits are:
- Increased wall thickness
- Longer tool joints
- It uses more hard-facing
- It may have a long central upset section
Heavy Weight Drill Pipe Applications
- Reduces drilling cost (check also drilling cost per foot) by eliminating Drill Pipe failures in the transition zone.
- Significantly increases the performance of small rigs through the ease of handling.
- Provides substantial savings in directional drilling process by replacing most rigid drill collar string, reducing downhole drilling Torque and Drag. Therefore, we can use them for high-angle drilling because it is less rigid than drill collars and has a much lower wall contact area, possibly reducing torque.
- We can use them for slim hole drilling because they have less chance of differential sticking than drill collars. The contact area for unstabilized drill collars is the full length of the collars, whereas HWDP has a contact area equal to the length of the tool joints and the wear pad (normally about 6ft per joint).
- Normally, we use them as a gradual transition between DC and DP to make the crossover gradual. HWDP is more fatigue-resistant than standard drill pipe, especially in compression.
Other Advantages Of HWDP
- It permits high-speed drilling with less torque, which reduces drill stem wear and tear and simplifies directional control.
- Pipe Tripping is faster than drill collars because HWDP is handled like normal DP.
- There is no loss of BOP control when handling HWDP since pipe rams can be used around it.
- Heavy wall drill pipe can be ordered as spiral or flush wall pipe.
Heavy Weight Drill Pipe Specifications
The Heavy-weight drill pipe specs vary for different manufacturers. Typical dimensions are shown in the below table:
HWDP Standards
- Quality Standard: API 7 and API 5DP.
- Steel Grade: Integral heavy-weight drill pipe: AISI 4145HM; Welded HWDP: AISI 1340.
- Pipe body, AISI 4140HM.
- Outer Diameter: 2 7/8” – 6 5/8”.
- Weight Range: 6.27#/FT through 27.72#/FT.
- Lengths: Range 2 and Range 3.
- End Finishes: Internal Upset, External Upset, Plain End Upset, Non Upset.
- Heavy Weight Drill Pipe Tool Joint type: NC38, NC46, NC50, 5-1/2 FH.
Specs Table
OD(in) | Connection | TubeID (in) | Adjusted Weight (lb/ft) | Tool/Joint OD (in) | TJ ID (in) | TJ Yield (ft-lbs) | M/U Torque (ft-lbs) | Prem Tube Tensile (lbs) | Type | Design |
---|---|---|---|---|---|---|---|---|---|---|
3 1/2 | NC38 | 2 1/4 | 23.29 | 4 3/4 | 2 1/4 | 19,200 | 9,600 – 11,520 | 237,600 | Standard | Conventional |
3 1/2 | NC38 | 2 1/4 | 23.29 | 4 3/4 | 2 1/4 | 17,600 | 8,800 – 10,560 | 621,000 | Integral | Conventional |
3 1/2 | NC38 | 2 1/4 | 29.72 | 4 3/4 | 2 1/4 | 19,200 | 9,600 – 11,520 | 237,600 | Standard | Spiral |
3 1/2 | NC38 | 2 1/4 | 23.73 | 4 7/8 | 2 1/4 | 22,900 | 11,450 – 13,740 | 237,600 | Standard | Conventional |
3 1/2 | NC38 | 2 1/4 | 30.16 | 4 7/8 | 2 3/8 | 22,900 | 11,450 – 13,740 | 237,600 | Standard | Spiral |
3 1/2 | NC38 | 2 1/4 | 25.36 | 4 7/8 | 2 5/16 | 22,900 | 11,450 – 13,740 | 237,600 | Standard | Tri-Spiral |
3 1/2 | NC38 | 2 1/4 | 26.55 | 5 | 2 1/4 | 24,800 | 12,400 – 14,900 | 237,600 | Standard | Conventional |
3 1/2 | HT38 | 2 1/4 | 25.36 | 4 7/8 | 2 1/4 | 34,200 | 12,900 – 20,500 | 237,600 | Standard | Tri-Spiral |
3 1/2 | HT38 | 2 1/4 | 30.39 | 4 7/8 | 2 9/16 | 29,400 | 12,200 – 17,700 | 237,600 | Standard | Spiral |
4 | XT38 | 2 9/16 | 29.38 | 4 3/4 | 2 9/16 | 31,300 | 11,500 – 18,800 | 407,600 | Standard | Tri-Spiral |
4 | TT390 | 2 9/16 | 28.81 | 4 7/8 | 2 9/16 | 46,100 | 23,000 – 32,300 | 407,502 | Standard | Conventional |
4 | XT39 | 2 9/16 | 28.24 | 4 7/8 | 2 9/16 | 37,000 | 12,400 – 22,200 | 407,600 | Standard | Conventional |
4 | XT39 | 2 9/16 | 29.99 | 4 7/8 | 2 9/16 | 37,000 | 12,400 – 22,200 | 407,600 | Standard | Tri-Spiral |
4 | XT39 | 2 9/16 | 29.82 | 4 7/8 | 2 9/16 | 33,900 | 11,400 – 20,300 | 815,200 | Integral | Tri-Spiral |
4 | XT39 | 2 9/16 | 29.26 | 4 7/8 | 2 9/16 | 33,900 | 11,400 – 20,300 | 815,200 | Integral | Spiral |
4 | XTM39 | 2 9/16 | 28.69 | 5 | 2 9/16 | 31,000 | 15,500 – 18,600 | 667,000 | XD-90 | Conventional |
4 | XT39 | 2 9/16 | 28.69 | 5 | 2 9/16 | 40,800 | 14,700 – 24,500 | 407,600 | Standard | Spiral |
4 | HT40 | 2 9/16 | 28.69 | 5 | 2 9/16 | 28,500 | 10,700 – 17,100 | 815,200 | Integral | Conventional |
4 | HT40 | 2 9/16 | 30.48 | 5 | 2 9/16 | 28,500 | 10,700 – 17,100 | 815,200 | Integral | Tri-Spiral |
4 | WT38 | 2 9/16 | 28.69 | 5 | 2 9/16 | 43,300 | 9,000 – 21,000 – 31,500 | 815,200 | Integral | Spiral |
4 | XTM39 | 2 9/16 | 28.69 | 5 | 2 9/16 | 37,200 | 18,600 – 22,300 | 407,600 | Standard | Spiral |
4 | XTM39 | 2 9/16 | 28.69 | 5 | 2 9/16 | 34,100 | 17,000 – 20,400 | 815,200 | Integral | Conventional |
4 1/2 | GPDS40 | 2 3/4 | 38.03 | 5 1/4 | 2 3/4 | 33,300 | 16,700 – 20,000 | 548,100 | Standard | Conventional |
4 1/2 | Delta425 | 2 3/4 | 37.23 | 5 1/4 | 2 3/4 | 51,400 | 25,700 – 36,000 | 548,060 | Standard | Conventional |
4 1/2 | Delta 425 | 2 3/4 | 37.50 | 5 3/8 | 2 3/4 | 56,000 | 28,000 – 39,200 | 548,060 | Standard | Conventional |
4 1/2 | XTM40 | 2 3/4 | 36.85 | 5 1/4 | 2 3/4 | 38,200 | 19,100 – 22,900 | 1,096,100 | Integral | Conventional |
4 1/2 | TT-485 | 2 3/4 | 43.31 | 6 1/4 | 2 3/4 | 108,000 | 49,800 – 64,786 | 548,100 | Standard | Tri-Spiral |
4 1/2 | XTM40 | 2 11/16 | 39.53 | 5 1/4 | 2 11/16 | 40,000 | 20,000 – 24,000 | 1,125,500 | Integral | Tri-Spiral |
5 | XT50 | 3 | 51.66 | 6 1/2 | 3 | 98,300 | 31,000 – 59,000 | 691,200 | Standard | Tri-Spiral |
5 | NC50 (4-1/2″ IF) | 3 | 57.93 | 6 1/2 | 3 | 52,000 | 26,000 – 31,200 | 1,382,300 | Integral | Spiral |
5 | XT50 | 3 | 49.77 | 6 5/8 | 3 | 105,300 | 35,100 – 63,200 | 691,200 | Standard | Conventional |
5 | NC50 (4-1/2″ IF) | 3 | 57.93 | 6 5/8 | 3 | 53,000 | 26,500 – 27,500 | 1,382,300 | Integral | Spiral |
5 | NC50 (4-1/2″ IF) | 3 | 49.77 | 6 5/8 | 3 1/16 | 56,500 | 28,250 – 33,900 | 691,200 | Standard | Conventional |
5 | NC50 (4-1/2″ IF) | 3 | 58.55 | 6 5/8 | 3 1/16 | 56,500 | 28,250 – 33,900 | 691,200 | Standard | Spiral |
5 | NC50 (4-1/2″ IF) | 3 | 52.34 | 6 5/8 | 3 1/16 | 56,300 | 28,150 – 33,700 | 691,200 | Standard | Tri-Spiral |
5 1/2 | XT54 | 3 1/4 | 57.57 | 6 5/8 | 3 1/4 | 93,200 | 26,600 – 55,900 | 1,700,900 | Integral | Conventional |
5 1/2 | TT550 | 3 1/4 | 57.57 | 6 5/8 | 3 1/4 | 850,400 | 56,800 – 68,200 | 850,400 | Standard | Conventional |
5 1/2 | Delta 544 | 3 1/4 | 58.41 | 6 5/8 | 3 1/4 | 86,600 | 43,300 – 52,000 | 850,438 | Standard | Conventional |
5 1/2 | HT55 | 3 1/4 | 60.13 | 7 | 4 | 77,200 | 33,600 – 46,300 | 850,400 | Standard | Conventional |
5 1/2 | XT57 | 3 1/4 | 59.51 | 7 | 4 | 106,200 | 36,400 – 63,700 | 850,400 | Standard | Conventional |
5 1/2 | HT55 | 3 1/4 | 60.87 | 7 1/8 | 3 5/16 | 105,700 | 40,600 – 63,400 | 850,400 | Standard | Conventional |
5 1/2 | HT55 | 3 1/4 | 60.87 | 7 1/4 | 3 1/4 | 105,500 | 41,600 – 63,500 | 1,700,900 | Integral | Conventional |
5 1/2 | 5 1/2″ FH | 3 1/4 | 62.27 | 7 1/2 | 3 5/16 | 78,500 | 39,250 – 47,100 | 850,400 | Standard | Conventional |
5 1/2 | 5 1/2″ FH DSTJ | 3 1/2 | 55.62 | 7 | 3 1/2 | 85,200 | 30,100 – 44,900 | 1,555,100 | Integral | Conventional |
5 1/2 | HT55 | 4 | 55.24 | 7 1/8 | 4 | 77,500 | 33,800 – 46,500 | 615,600 | Standard | Spiral |
5 7/8 | XT57 | 4 | 55.14 | 7 | 4 | 106,200 | 36,400 – 63,700 | 799,800 | Standard | Conventional |
5 7/8 | XT57 | 4 | 57.42 | 7 | 4 | 106,200 | 36,400 – 63,700 | 799,800 | Standard | Tri-Spiral |
5 7/8 | TT-585 | 4 | 56.93 | 7 | 4 | 116,500 | 58,300 – 69,900 | 799,800 | Standard | Tri-Spiral |
6 5/8 | 6 5/8″ FH | 4 1/2 | 73.59 | 8 1/2 | 4 1/2 | 75,000 | 37,500 – 45,000 | 1,021,600 | Standard | Conventional |
Download Heavy Weight Drill Pipe Specs Sheets
We have gathered specification sheets for each size of HWDP and collected them to be downloaded from the following link:
Heavy Weight Drill Pipe Selection And Design
Field tests indicated that fatigue build-up in the Drill Pipe in the transition zone is related to the relative stiffness of the Drill Collars and the adjacent Drill Pipe. The equation expresses the stiffness ratio of two sections of pipe in the drill string,
The field tests showed that the higher the stiffness ratio at the transition zone, the greater the fatigue build up. Criteria for permissible stiffness ratio vary between different operators and areas. The following maximums are typical:
- For shallow or routine drilling or low failure rate experience, keep the stiffness ratio below 5.5.
- For more severe drilling or significant failure rate experience, keep SR below 3.5.
In conclusion, to enhance the service life of the drill pipe and decrease the stiffness ratio, a Heavy Weight Drill Pipe (HWDP) is used between the drill pipe and drill collars. The HWDP has the same outer diameter as the drill pipe, with a wall thickness of up to 1 inch and a weight of up to 78 lb/ft. Depending on the specific drilling operation, the number of HWDP joints used ranges from 15 to 21.