The most commonly used technique for changing the trajectory of the wellbore uses a piece of equipment known as a “bent sub,” which is used only in directional well drilling (Figure 1) with a Positive Displacement (mud) motor.
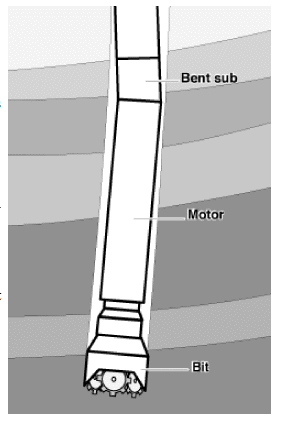
What is The Bent Sub In Directional Drilling
A bent sub (Drilling Subs) is a short length of pipe with a diameter approximately the same as the collars and threaded connections on either end. It is manufactured in such a way that the axis of the lower connection is slightly offset (less than 3 degrees) from the axis of the upper connection. When made up into the Bottom Hole Assembly BHA, it introduces a “tilt angle” to the elements of the BHA below it and, therefore, to the axis of the drilling bit.
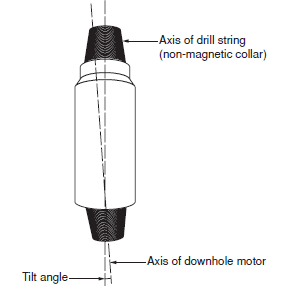
However, the introduction of a bent sub into the Directional BHA means that the center of the bit is also offset from the center line of the drill string (Check Drill String Design Calculation) above the bent sub, and it is not possible, therefore to rotate the drill bit by rotating the drill string from surface. Even if this were possible, the effect of the tilt angle would be eliminated since there would be no preferential direction for the bit to drill in. Therefore, the bent sub must be used with a Positive Displacement Motor, PDM, or a Turbine.
How To Use Bent Sub With Directional Mud Motor
The PDM is often called a mud motor and is used in far more wells than the turbine. The mud motor is made up into the Driling BHA of the drill string below the bent sub, between the bent sub and the bit. When drilling fluid is circulated through the drill string, the inner shaft of the mud motor, which is connected to the bit, rotates, and therefore the bit rotates. It is, therefore, not necessary to rotate the entire drill string from the surface if a mud motor is included in the BHA.
Mud motors and turbines are rarely used when not drilling directionally because they are expensive pieces of equipment and do wear out.
A scribe line is marked on the inside of the bend of the bent sub, and this indicates the direction in which the bit will drill (this direction is known as the “toolface”). A directional surveying tool (often an MWD tool) is generally run as part of the BHA (check our survey calculation guide) just above the bent sub so that the well trajectory of the well can be checked periodically as the well is deviating.
The Major Disadvantage Of The Bent Sub
The bent sub and PDM can, of course, only be used in the build-up or drop-off portion of the well since the bit will continue to drill in the direction of the tilt angle as long as the bent sub is in the assembly and the mud motor is being used to rotate the bit. This leads to the significant disadvantage of using a bent sub and PDM to change the trajectory of the well.
When drilling a well, the “conventional” assembly (without a bent sub and mud motor) used to drill the straight portion of the well must be pulled from the hole, and the bent sub and PDM assembly run in the hole before the well trajectory can be changed.
The bent sub and motor will then drill off in a particular direction. When the well is drilling in the required direction (inclination and azimuth), the bent sub and PDM must then be pulled and the conventional assembly re-run. Otherwise, the drill bit would continue to change direction. This is a very time-consuming operation (taking approximately 8 hrs at 10,00 ft depth for each trip out of and into the hole). Remember, however, that the build-up section of a well can be 1-2000 ft long depending on the build-up rate (typically 1-3 degrees/100ft) and the required inclination. Therefore, depending on the penetration rate, the bent sub and mud motor will be, depending on the rate of penetration, in the well for quite a long time.
Running Procedures
Firstly, Inspect the motor and then test using standard procedures.
- Before drilling can begin with a motor and bent sub-assembly, orient the bent sub (tool face) in the desired direction.
- Work the pipe until string torque is eliminated. The best results are obtained by using a moderately fast up-and-down pipe movement. It is recommended that the bit be kept at least 5 feet from the bottom of the hole.
- Make a reference mark on the kelly bushings, lock the rotary table, and take a survey to determine tool face orientation.
- Turn the drill pipe to achieve the desired tool face orientation. This orientation should include an allowance for the anticipated left-hand reactive torque.
- When orienting, turn the pipe to the right unless the turn is less than 90° left of the present setting.
- Work the string up and down so that the turn reaches the bottom hole assembly.
- Lock the rotary table before beginning to drill.