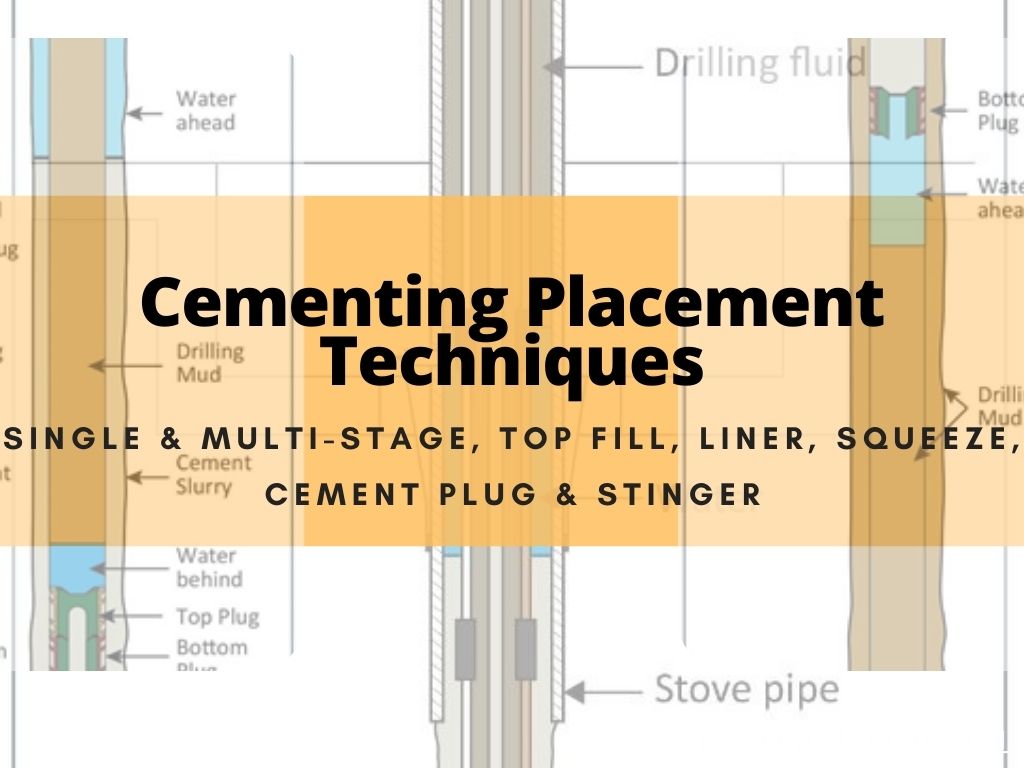
The complete removal of the mud from the annulus (Mud Conditioning Simple Guide For Better Cementing) and its replacement with a good cement slurry is the major requirement for a good cement job. Cement placement is influenced by:
- Drilling fluid condition,
- The presence of a good spacer(s),
- Casing/pipe movement,
- Displacement velocity,
- Cement Slurry properties,
- Casing/pipe centralization in the hole.
- Contact time.
Good cement placement can only be achieved when all parameters are optimally fulfilled.
Single Stage Cement Jobs
Single-stage cementing jobs are routine and straightforward. The procedure is shown graphically in Figure 1.
- The pre-flush and spacer are pumped.
- The bottom plug is released.
- Cement slurry is mixed and pumped.
- The top plug is dropped.
- Post flush is pumped.
- Cement is displaced, usually using one or more rig pumps
Stinger Cementing
The cementing stinger (or inner string) method is used for relatively short, large-diameter surface casing where the hole size is not accurately known, losses to the formation may be or have been experienced, or to reduce the displacement volume and time of the cement placement job. The use of a small capacity cement stinger (usually drill pipe), allows for flexibility in the quantity of cement used, whereas conventional methods use a fixed pre-calculated volume of cement which is mixed and displaced.
Multiple Stage Cementing Placement Method
Two-Stage cementing places more than one batch of cement behind the same string of casing at selected depths.
The applications of stage cementing include:
- Cementing a very long interval, with reduced pressure on formation and equipment.
- Cementing off formations at any point e.g. placing cement above a loss zone.
- Minimizing the loss of cement slurry to weak formations.
- Reduction of channeling.
- Less risk of flash setting during chase caused by cement dehydration.
Stage cementing uses a special collar installed on the casing string. The collar is positioned at the required depth of the bottom of the second batch of cement. When using a conventional stage collar there will usually be a short overlap of cement – the first stage top of cement will be planned to end just above the stage collar.
The stage cement collar tool incorporates ports that allow flow between the inside and the outside of the casing. Two methods are used to open the collar. Mechanical systems use a free-fall opening tool which is dropped after the first stage job has been completed. Once it has seated, pressure is applied to open the sleeve.
Liner Cementing Placement
The liner running and cementing process is illustrated in Figure 30.
- Make up and run the liner hanger, check floats, circulate 120% casing liner string contents, and install the hanger seal assembly and running tool. Note the weight of the liner. This can then be used to check that the string weight has decreased by the right amount after setting and releasing from the liner hanger system.
- Run to the bottom, filling the drill pipe with drilling fluid.
- Establish circulation carefully and circulate bottoms up.
- Set the liner hanger by reciprocation and rotation for a mechanical set hanger, or drop and displace the setting ball and pressure up the drill pipe and pump out the sleeve of the hydraulic set hanger.
- Disengage the liner running tool by rotation and confirm that the drill pipe is mechanically free from the liner by picking up and checking the hanging weight.
- Install the cement head. Mix and pump cement.
- Release the drill pipe wiper plug and displace it. When this plug reaches the liner wiper plug, the latter will shear and the combined plugs are then displaced to the liner baffle collar.
- Set the liner/casing seal by set-down weight for a mechanical type or by pumping against the landed displacement plugs for the hydraulic setting tool.
- Pick up the drill pipe running string. The presence of cement above the liner should be indicated by pressure on the drill pipe after the running tool has been pulled out of the liner. Circulate out excess
Outside Cementing (Top Fill) Placement Method
When cementing the surface string it frequently proves difficult to get cement to the surface. A low TOC may create problems such as insufficient support for the rest of the well, buckled casing, or an annular pressure build-up due to influx from a shallow gas pocket.
To remedy such a case outside or annular cementing may be used. In this technique, a small-bore pipe is run into the annulus through which cement can be pumped. Thixotropic cements are used to keep the cement volume more or less intact during the gelling and setting stage. Metal petal baskets are sometimes used to provide a base for the top fill cement job.
Setting Cement Plugs
A cement plug is a volume of cement designed to fill a length of casing or open hole and provide a seal against vertical fluid movement. Common uses of cement plugs are:
- To plug and abandon an entire well.
- To provide a kick-off point for drilling sidetracking operations.
- To abandon lower depleted zones in a completed well.
- To isolate a zone for formation testing.
- To seal off lost circulation zones
- To temporarily isolate a zone to protect it during workover
Squeeze Cementing
Squeeze cementing involves forcing a cement slurry through holes in the casing. The primary objective of squeeze cementing placement method is to develop a seal in the casing-well bore annulus between formation intervals penetrated by the casing. The most common reasons for squeeze cementing are:
- To repair primary cement jobs that failed due to channeling or insufficient cement height in the annulus.
- To shut off perforations in a depleted interval by filling the perforation tunnels and surrounding formation with cement.
- To reduce unwanted gas or water influx by selectively squeezing-off perforations.
- To plug all or part of one or more zones in a multi-zone injection well in order to direct injection into desired intervals.
- To repair casing leaks.
Achievement of the squeeze cementing objectives and features in line with the proposed job technique is quite useful tools towards successful cementing operations. selective of the right squeeze cementing method that is applicable to rectify any primary cementing job failures is recommended. Casing Leaks can be rectified and repaired so as to avoid gas migration and provide casing support through proper remedial cementing operation. It is recommended to select the most economical squeeze cementing methodology as applicable.