Before approving a drilling program, the drilling team must perform estimation for the overall costs of the oil well drilling operations. Suppose there is no previous drilling data in a new area. In that case, the drilling team can only approximate the well cost roughly. In most cases, the drilling team can use available well data to make a reasonable approximation.
It is clear that to be able to accept the responsibilities of estimation for oil well drilling cost, the drilling team needs to:
- Have a thorough understanding of cost elements related to the well-engineering function,
- Capture and record in an accurate and timely fashion the operating costs of all activities.
- Use these data to produce reports and cost indicators, enabling them to measure, understand, and improve the cost-effectiveness of the operations.
- Apply the same general principles to the budgeting process to monitor operating and drilling costs.
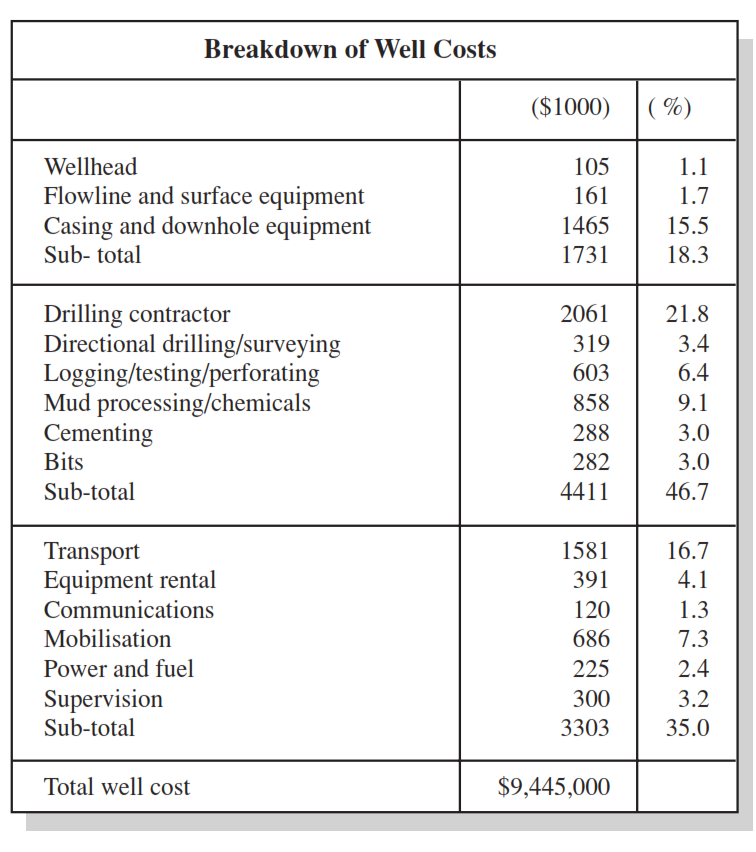
Well Engineers, Civil Engineers, Transport Supervisors, and other involved parties must understand the different cost elements. The drilling team needs to provide the actual values of lump sums and unit rates that apply to their operation.
Types of Oil Well Drilling Costs Estimation
We use drilling cost to refer to all equipment and operations expenses required to make a well for hydrocarbon production, such as the storage of equipment and equipment maintenance. Resources such as capital, fixed, and variable costs are also referred to. Capital costs include well-planning and construction costs. Furthermore, there are two types of fixed costs: dependent costs and independent costs. For example, we can classify wellheads and mobilization as dependent costs. However, we can consider also safety valves and drill string costs as independent costs.
There is also another term which we call the variable costs. These costs are a function of time, such as fuel and power needed daily. Regardless which product or service we will use, we can subdivide drilling costs into three elements.
- Rig Costs
- Tangible type
- Services expenses
There is also another classification of well drilling costs as follows:
- Time-dependant.
- Depth-dependant.
Rig costs
Rig cost refers to hiring a drilling rig and its equipment from a service company. This cost can make up 50-70% of the total well cost. Oil & Gas Companies typically express rig cost as a daily rental rate, which depends on various factors such as the rig type, market demand, the duration of the rental period, and the contract length.
Please note that when estimating a well’s total cost, it is necessary to consider well completion type and dry hole costs for development and appraisal wells.
Tangible costs
Tangible costs include well products such as casing pipe, cementing, tubing, and completion equipment. When purchasing, the drilling engineer must consider the factors contributing to each product’s price. For example, when buying casings to insert into the hole, you must consider their size, temperature, and pressure grades. Remember, if we deduct 100% of tangible drilling costs, it will make an investor’s day.
Service costs
Generally, the Service Company performs certain operations during drilling that the operator company does not undertake. Those operations include:
- Preparing mud materials and engineer
- Wireline logs
- Solids control equipment
- Directional Drilling
- Cementing
- Wellhead services
- Mud logging services
- Fishing In Drilling Services
Companies use the drilling and completion services index to predict the cost of drilling tools, including products and services for Drilling and completion. It includes the recent cost survey and the future cost changes by quarter for the upcoming year for:
- Drilling rigs (Check drilling rig components)
- Drilling bits
- Completion rigs
- Stimulation services
Time-Dependent Costs
Time-dependent costs fall into the following categories:
- Drilling Contract payments
- Personnel
- Consumables
- Service fees
- Company overheads
Contract Payments
All contractual payments for services applicable during the contract period of the rig, specified as a daily rate, are included in the time-related costs. For example:
- Rig crew hire and rates
- Cementing
- Diving
- Wireline logging
- Geological surveillance
- Drilling/Completion fluid engineering
- Telecommunications
- Transport on/offshore
- Insurance
- Tool rental.
The service providers mainly specify a daily rate for equipment rental and execute a specific activity with that equipment. The latter usually will be converted to a daily rate costs for oil well drilling estimation purposes.
Personnel
The costs associated with a particular well are time-dependent and include expenses for the assigned Company personnel. When office-based operations staff work on only one well, they charge all of their costs to that well. Small businesses or individual departments with limited resources usually operate under this condition. However, in larger units where there is a need to drill more than one well simultaneously and prepare work for future wells, allocate the staff costs to each well based on the time spent.
Examples of the office-based personnel meant here are:
- Operations Manager
- Head of Well Operations
- Site Drilling Supervisor
- Well Engineers
- Civil Engineer (if solely concerned with access road and location construction/rehabilitation)
- Administrative assistants in the Well Engineering Department
- Â Geologists
- Company Mud Engineers
In an OU solely engaged in drilling activities, i.e., an exploration company should include Materials/Transport staff in this list. If undertaking production or engineering activities, we would treat them the same way as non-operations staff.
Consumables
The cost per day for consumables usually only includes payments for the fuel and lubricants for the rig, supply vessels, standby vessels, and helicopters if they still need to be covered by the day rates for contract payments.
The sum of the above-mentioned time-dependent costs is often called the DAILY OPERATING COST for the rig.
In below graphs will provide the daily operating cost for various types of rigs. It is only given as an indication; any figures quoted would be out of date within a month.
Data Compiled Sept 12, 2023
Data Compiled Sept 12, 2023
Company Overheads
Costs allocated to company overhead include expenditures by departments providing services to other “customer” departments. In some cases, we may charge all overhead costs to the current drilling well costs (but still under the heading “overheads.” In other cases, they may be treated differently, either as an independent budget item or by being allocated among the “client” departments utilizing a time-based system of internal fees.
Examples of the type of expenditure covered by such overheads are:
- The salaries of administrative staff.
- The cost of housing.
- Office rental.
- The rental of yard space, wharves, and warehouses.
- The price of company vehicles.
- The cost of airfares for company personnel.
Depth-Dependent Costs
Costs for depth-dependent items are those payments for equipment and consumables that are used or remain downhole. These items include:
- Bits.
- Casing and casing attachments.
- Cement, additives and Cementing tools.
- Mud chemicals and lost circulation materials.
- Completion of tubing and attachments.
- The Completion of fluids and chemicals.
Depth-dependent costs can vary from approximately 350 to 600 US$/meter of well depth depending on whether the well is on- or offshore and in a remote area.
Fixed/Once-Off Costs
It’s important to note that in addition to costs that vary with time and depth, other costs can make up a significant portion of the total well costs. These costs are known as fixed or once-off costs. Fixed costs are typically a one-time payment specified in a contract, while once-off costs are expenses that occur just once per well. We don’t know the exact amount of a once-off cost in advance.
Fixed Costs
The costs for mobilizing a rig and all related service contract equipment and personnel from one part of the world to another are very much dependent on the move distance, rig type and how the transport is to take place. This is usually specified as a fixed amount in the contract(s) and can be 20,000 $ to 4 million dollars, depending on the circumstances.
Another example of a fixed cost would be drilling one (or two) water wells per location or group of sites for a fixed price.
It is mandatory to distribute the fixed costs independent of the number of drilled wells, such as mobilization expenses, equally among all wells that benefit from the expenditure.
There are two ways to charge for rig-moving: a fixed price or a unit rate per kilometer. If you charge by the kilometer, consider it a one-time cost. When moving a rig from one well to another, charge all fees associated with the move to the new well. It’s worth noting that this approach differs from the usual practice of sharing mobilization and demobilization costs among all the wells.
Once-Off costs
In new areas, all facilities that have to be set up expressly for the execution of a project are once-off costs charged to the well or wells that are to be drilled. These can, especially in remote areas, be the costs for installing an infrastructure such as office construction, installation of the long-distance telephone network, etc… (Usually, established companies charge these costs to overheads.).
As mentioned above, we can classify the reconnaissance visits and audits as once-off costs. In addition, we can distribute the price of a reconnaissance visit equally among the drilled wells. However, we can typically charge the fee of an audit to the current drilled well.
Building drilling locations and access roads costs for onshore wells are “well specific” and added to the well account as once-off costs. The same would apply to water wells if they are drilled on a unit rate basis (but the mobilization of a water well drilling unit would still be a fixed cost). For an offshore drilling rig operations, the expenses related to seabed surveys, seabed preparation, and rig positioning are similarly once-off
Other than the cases mentioned above, once-off costs relate to non-time- and non-depth-dependent costs for permanent well equipment and work undertaken for a specific well only. The primary item is the wellhead and its related equipment. If recovering the wellhead, often with exploration wells, the costs allocated to the well are those of refurbishment and depreciation.
Budgets & Cost Reporting
The prime purpose of any budget is to serve as a vehicle to secure the funds necessary to execute a given activity. In addition, a budget is a vital tool for monitoring and controlling costs. For this to happen, preparing a budget requires the same attention to detail as reporting operating and drilling costs.
To produce realistic and justifiable budget proposals, reliable cost data for historical performance must be available.
Therefore, Drilling and completion costs, broken down as we described above, are of fundamental importance. Therefore, It is mandatory to monitor, report, and record them. Usually, the daily activity reporting system includes this data, which requires the Site Representative to enter the cost data for services, well equipment, consumables, and operations details.
With the available well cost data, the comopany can set a well cost database has been set up in the company. In addition, We can use it for the estimation for the future oil well drilling costs based on historical performance.
Total Well Drilling Cost
Generally, we can break down the total drilling cost into three main areas: preparation, Drilling, and completion. Each has a specific contribution to the entire well drilling cost, as shown in Figure 3. Preparation refers to site preparation, such as water, electricity supply, and surface casing, and it covers approximately 18% of the total well cost. Drilling has the highest contribution to the well cost, which is 73% of the total well cost. In the final stage, completing the well covers the remaining fee (9%).
A sub-classification would further classify the cost of drilling a well to perforations, well loggings, cementing…etc. All of those sub-classifications are categorized under the breakdown of well cost three components.
Cost Estimation
Figure 2 shows a typical cost distribution for a North Sea Well. Some costs are related to time and are therefore called time-related costs (e.g., drilling contract, transport, accommodation). Many consumable items (e.g., casing, cement) are related to depth and are often called depth-related costs. We can estimate these costs from the drilling program, which gives the lengths or volumes required. Some consumable items like the wellhead will have a fixed cost. In addition, we shall charge the drilling services (e.g., perforating) based on the current service contract. The price list associated with this contract will be a function of time and depth. Furthermore, the payment for the service will be made when the operation has been completed.
The Conceptual Estimate
- This is required in a feasibility study to determine whether a venture is economically viable.
- Very limited well requirements will be available; probably only the approximate TD, the primary lithology, and a location description (desert, water depth).
- It is crucial to make many assumptions, and the expected accuracy is no more than ±40%.
- Oil Well historical data is usually the basis for this drilling cost estimation, with adjustments made for location differences between the historical and the proposed area and variations in the market costs for equipment and services.
The Budget Estimate For Oil Wells
This typically aims to calculate the annual expenditure included in the Company Business Plan. Although the actual well program is unlikely to have been prepared, more information will be available than for the conceptual estimate.
As a result, we can use a combination of historical costs and local information to compile a simplified drilling cost breakdown along the lines described above. The accuracy required for this estimate is 15% to 20%. In addition, the accuracy may change from company to other according to their policy.
The Estimation Of Oil Well Drilling Cost
Generallu, well cost estimate is the last estimate before drilling the oil or gas well. A well proposal, a well program, a detailed design, and the costs related to specific service contracts need to be available to meet the accuracy requirements of this estimate.
It is this estimate on which the Approval For Expenditure (AFE) will be based. It becomes the reference cost for the end-of-well reconciliation of actual and planned well costs.
Comparing actual well costs to cost estimates can increase efficiency in future wells. Such differences can be due not only to estimating errors or cost variances but also to performance variances. Therefore, modifying and tunning the future operations is necessary to have a better performance and efficiency.
Making The Estimate
Break down a cost estimate into minor elements for which individual estimates can reasonably be made based on available information. Initially, this involves more work than “broad brush” estimates, but it will save time and effort in the long run.
There are several reasons:
- It reduces the uncertainty that must be built when combining historical costs with specific circumstances. Finding a precedent for each element will usually be possible in any given situation, but not necessarily from the same historical operation.
- As explained in the previous sub-topic, the cost estimate for a well begins with a rough estimate. It gets more accurate as more information becomes available. The final well cost estimate is made only after all the contracts have been awarded and the pricing has been fixed. The additional information that becomes available helps to refine the cost of individual elements. Updating and refining the estimate as new data arrives is then a question of a few minutes if it is a matter of changing one unit rate figure for another. However, there would be no logical method for updating an estimate made globally.
- It is a fact of life that the Well Engineer will have to make cost estimates based on insufficient information. Estimation of the individual oil well cost elements and then summing them enables the known data to be included and the uncertainties of the remaining drilling data to be quantified. The resulting cost estimate, expressed as a range, can be justified and accepted by the management, whereas quoting unjustifiable figures would not.
It is always necessary to include a “miscellaneous” category for small amounts of expenditure that do not fall into the other types. However, this should be restricted to a meager amount and not used as a safety net for inaccuracies in the estimates of specific elements.
References
- Cost Estimation For Well Drilling Design
- Al Kindi, Mahmood & Al Lawati, Malak & Al-Azri, N.. (2017). Estimating Drilling Cost and Duration Using Copulas Dependencies Models. The Journal of Engineering Research [TJER]. 14. 1. 10.24200/tjer.vol14iss1pp1-9.
- Kaiser, Mark. (2007). A survey of drilling cost and complexity estimation models. International Journal of Petroleum Science and Technology ISSN Number. 1. 973-6328.