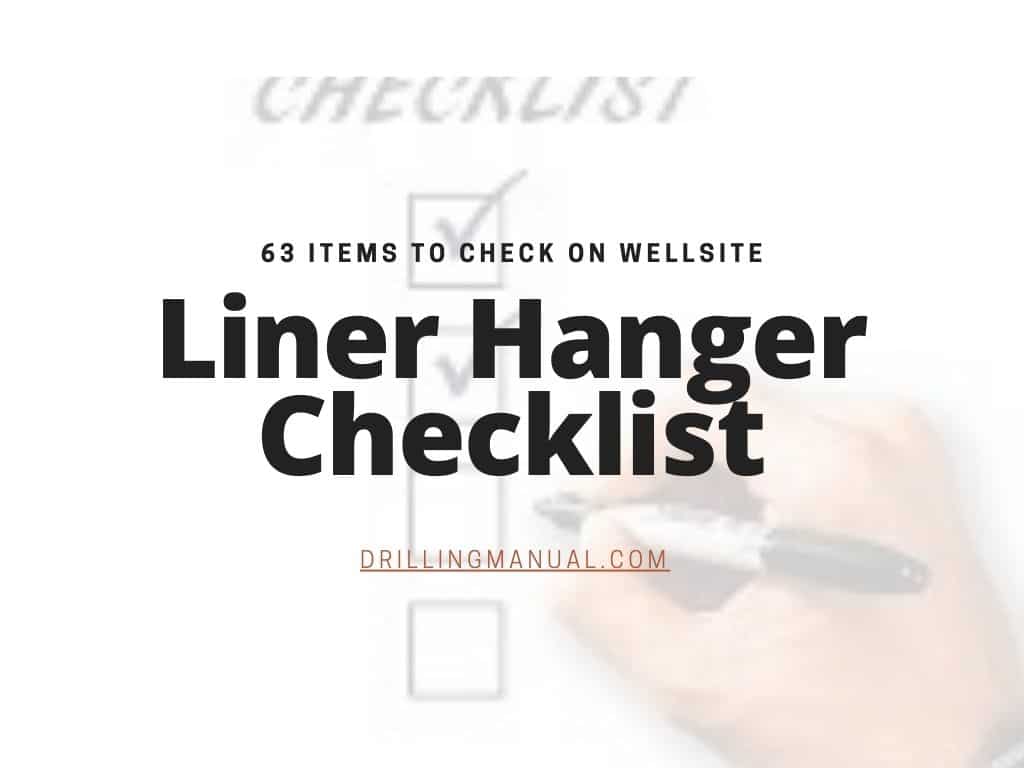
This is a minimal checklist to be made at the well site to ensure the equipment is correct, not damaged in shipment, and that all necessary tools have been received at the well site. You are making the final check. Do not assume all things are correct. Make all checks physically possible to ensure the success of the job.
- Physically check and record drill pipe (tech-fact S/2 pg.10) size weight grade thread ID
- Physically check and record drill pipe (2 nd string of pipe) size weight grade thread ID
- Check the drilling talley (DP, BHA, + Kelly Dn.) to ensure TD is where you were told it was!
- Number of joints on location Stands in derrick
- Check with customer and record casing size weight grade thread ID
- Check with the customer and record intermediate liner size weight grade ID
- Will all equipment being run pass into intermediate casing/casing liner (yes-no)
- Physically check and record liner size weight grade thread ID
- Did you measure the length of the liner (yes –no) Talley the liner strap (yes–no)
- Total number of liner jts on location jts.
- Physically check and record hanger size weight grade thread cone OD
- Physically check liner hanger operating mechanism (mechanical hanger) (yes/no)
- Look up hanger load capacity and record lbs.
- Physically check hanger shear pins size total number of pins pressure to shear pins psi.
- Physically check liner packer shear pins total number of pins setting force to shear pins lbs
- Physically check liner tieback extension OD. ID collapse burst
- Physically check setting tool for obstructions (yes –no)
- Physically check setting tool thread type (yes/no)
- Compatible with customers pipe (yes/no) If not, physically check x-overs needed to run tools(yes–no)
- Physically check pump down plug/cementing plugs size (yes/no) Compatible with customers drill pipe (yes/no)
- Does plug(s) fit liner wiper plug(s) and/or landing collar? (yes/no)
- Physically check liner wiper plug/plugs size ID
- Will plug/plugs pass thru all accessories in liner string (yes/no)
- Physically check setting ball size type (bronze, kirksite, bake-lite, Rogers)
- Physically check setting ball in Type II landing collar (yes/no) Ball seat ID
- Physically check x-over bushings or x-over Jts. for compatibility with liner (yes/no)
- Physically check landing collar, float collar and shoe for compatibility with liner (yes/no)
- Physically check all your equipment for damages (yes/no)
- Will RS/polished bore receptacle pack off come back thru ZXP packer and/or liner hanger (see warehouse drawing) (yes/no)
- What is the effective stroke of the packer setting dog sub (Drilling Subs) ft.
- What is the effective stroke of the slick stinger ft.
- What is the effective stroke of the sleeve/pbr pack off ft.
- Physically check plug dropping cementing head and accessories threads (yes/no) compatible with customers pipe (yes/no)
- Physically check lift nipple for proper od (yes/no)
- Physically check low torque valve operate freely (yes –no)
- Physically check wheel valve (yes/no)
- Physically check swivel turns freely (yes/no)
- Physically check hammer unions are tight (yes/no)
- Physically check flag sub trigger operation (yes/no)
- Physically check ball dropping sub-operation (yes/no)
- Physically check T. D. head operation (yes/no) drop/lock handle (yes/no) flapper (yes/no)
- Did you install pump down plug (yes/no) if no, inspect to see if plug(s) are installed
- Physically check the safety bushing for proper threads to liner and drill pipe. (yes/no)
- Physically check lift nubbins for proper fit (yes/no) elevators, (yes/no) slips (yes/no)
- How many turbolators or centralizes is to be used turbolator od. are turbolator right hand left hand
(Note: right hand turbolators can release HR running tool and left hand can release 2-RH & C-2 Running tool.) - Was liner pipe drifted (yes/no) drift size
- Were you on the floor when drill pipe rabbit was dropped (yes/no) retrieved (yes/no)
- Was all the drill pipe , heavy weight , drill collars , x-over subs, jars, etc. to be used, drifted (yes/no)
- Give drift OD. ID. length
- Was the wear bushing pulled (yes/no) if no, bushing ID
- Did you recommend to thread locking the shoe track (yes/no) was it done (yes/no)
- Does drilling mud have LCM (yes/no) lbs per bbl recommend removing it from the system (yes/no)
- Does float shoe or self-filling float equipment operate properly (yes-no)
- After picking up hanger assembly was drill pipe wiper rubber installed on drill pipe (yes/no)
- Was PalMix installed in the sleeve? Is the pack-off below the running tool?
- Did “YOU” drop the ball and pump down plug? (yes-no) If no, explain.
- Did you make all calculations necessary to achieve a successful job (yes/no)3
- Were you on the rig floor when the setting tool was pulled thru table (yes-no) if no, explain
- Was setting tool complete when pulled (yes/no) any damage (yes/no) if yes explain
- Was service. breaks made at all tool joint connection of setting tool and head assembles (yes/no)
- Was shear indicator sheared on rotating dog sub (yes/no)
- Was all equipment put back in basket and inv. checked by you and clearly mark for return to the district
Check the explanation for each item from here (Explanation of Liner hanger checklist)
Hi
I am looking TRS JOB.
I am ex baker TRS in gabon ( Africa)