We can define the drill string as a group of pipes and accessories on which the drill bit is run to the bottom of the borehole. These components allow us to deliver the rotation, the weight, and the fluids from the surface to the bottom of the drilled hole. It is an important part of the rotary drilling process in oil and gas wells. To understand more about it, we will have to go through three subjects :
- Its components
- Design
- Care of the string
The dimensions of a typical 9,000 ft drill string would be :
Components | OD | Length |
Drill Bit | 12 1/4″ | |
Drill Collars | 9 1/2″ | 600 ft |
Drill Pipe | 5″ | 8400 ft |
Drill String Functions
The Drill string components serve several purposes and functions, which include the following:
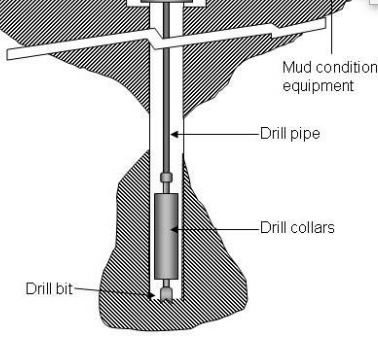
- The drill string Provides a fluid conduit from the drilling rig to the Drilling Bits.
- Also, it had another function: imparting rotary motion to the Drilling Bits.
- The existence of drill collars will provide the Weight On Bit (WOB) necessary to drill the hole.
- Lower and raise the Drilling Bits in the well.
- Drill String functions are a lot more, but it depends on what you must do. It can allow formation evaluation and testing, but special tools will do this for such applications.
Components Of Drill String
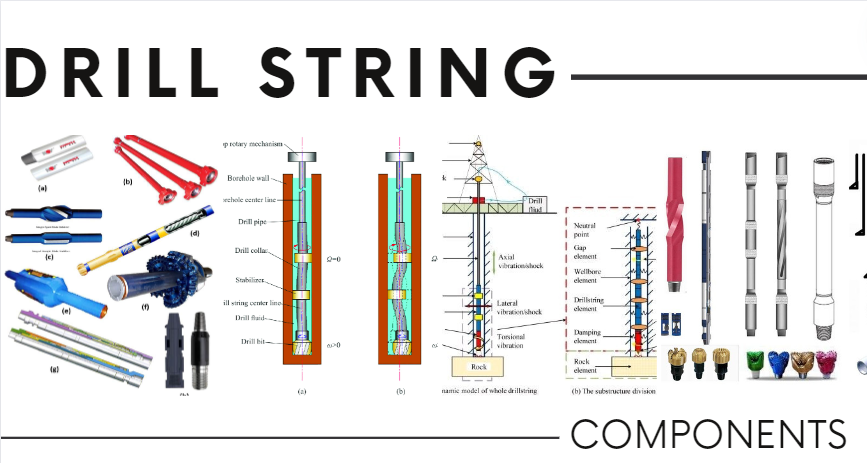
The major components of the drill string:
- Drill Pipe Tubular
- Transition pipe, which is often heavy-weight drill pipe (HWDP)
- Drill Collar
Drill Pipe
The drill string is made up of several sections, with the drill pipe being the longest. The Bottom Hole Assembly (BHA) is usually no longer than 1,000 feet. Each joint of drill pipe comprises of the pipe body and the tool joint, which connects the sections of drill pipe. At one end of the pipe is the box with the female end of the connection, while the male end of the connection, known as the pin, is at the other end of each length of the drill pipe. Drill pipe joints are available in three length ranges:
- The length of range 1: 18-22 ft
- The length of range 2: 27-30 ft
- The length of range 3: 38-45 ft
Drill pipe is available in various sizes and weights, as shown in Table 1. Some common sizes include the following:
- 5 in. -19.50 lb/ft nominal
- 4 ½ in.-16.60 lb/ft nominal
- 3 ½ in.-13.30 lb/ft nominal
Different types of drill pipe tool joints can increase the average weight per foot, i.e., 16.60-18.60 lb/ft for a 4.5-in. pipe. However, the pipe is still referred to as 16.60-lb/ft. The grade of the drill pipe is determined by its minimum yield strength, which is important for calculating its burst, collapse, and tension. The most common grades include:
Drill Pipe Specs
Tube OD, nominal weight, pipe grade, type of tool joint, thread connection, and classification generally describe drill pipe components. For example, a 5″ drill pipe can be described as,
5″ | 19.5 | Grade E | XH | NC50 | Premium Tube |
Outer Diameter | Nominal Weight | Minimum Yield Strength | Tool Joint Upset | Connection Thread | Wear Classification |
Each description item is explained in the API DRILL PIPES DESCRIPTION & SPECS Article.
Heavyweight Drill Pipes
The practice of using heavy-weight drill pipe in the drilling industry has gained wide acceptance. These pipes usually have a greater wall thickness than regular drill pipes. They are commonly utilized at the bottom of the drill pipe where there is a high stress concentration. The reason for this stress concentration is due to various factors, which are:
- The cross-sectional area of drill pipe and drill collars varies, which results in a difference in their stiffness.
- The bit’s rotation and cutting action often cause it to bounce vertically.
Considering the number of pipe joints that should be run in the transition zone is crucial. Based on successful field experience, using a minimum of 18 to 21 joints of HWDP between the drill collars and the regular drill pipe in vertical holes is recommended. It is common to use thirty (30) or more joints in directional holes.
Role Of HWDP In Drill String
Reduces drilling costs by virtually eliminating drill pipe failures in the transition zone.
- By replacing some drill collars, small rigs in shallow drilling areas can significantly increase their performance and depth capabilities.
- Absorb the stress transferred from the rigid drill collars to the comparatively flexible drill pipes.
- Less wall contact area between the pipe and hole wall reduces rotary torque, the chance of differential sticking, and vertical drag, improving directional control.
The article Heavy Weight Drill Pipe discusses in detail their specs and function.
Drill Collar Role In Drill String
Drill collars are tubulars that are heavy enough to apply weight to the drill bit. They help keep the drill string in tension, reducing bending stresses and failures caused by fatigue. Furthermore, drill collars provide stiffness in the bottom hole assembly (BHA), allowing for better directional drilling control.
In reality, not all drill pipe weight sits down on the drill bit. There is buoyancy in the mud, which reduces the downward force by around 20%. Also, because of the pipe’s long length, the drill string’s upper part is in tension, whilst the lower part is in compression. In fact, if we allowed all of the weight of the drill pipe to push down, it would buckle and twist and send the bit off drilling in the wrong direction.
Drilling engineers, therefore, calculate and find out exactly what part of the drill string weight will be sitting down on the bit. They also know the optimum weight for the particular bit in the type of rock they are drilling. Therefore, after these calculations, adding drill collars to the drill string just above the bit is common. Drill collars are heavy weight sections of drill pipe, they add just the right amount of additional weight to the bit and add it just behind the bit, giving the driller confidence that the bit is drilling in the desired direction.
Role and Significance of Drill Collars in Drilling Operations
Some of the functions of the collars are as follows:
- Provide weight for the bit.
- Minimize bit stability problems from drilling vibrations, wobbling, and jumping.
- Provide the strength needed to run in compression.
- Minimize directional control problems by providing stiffness to the BHA.
Types and characteristics of drill collars
There are several types of drill collars, each with specific characteristics and benefits for drilling operations.
Spiral drill collars are designed with a spiral groove on the outer surface to reduce the friction between the drill collar and the borehole, allowing for smoother and more efficient drilling. Nonmagnetic drill collars are made from non-magnetic materials, such as aluminum or titanium, to minimize interference with sensitive instruments used in drilling operations, such as magnetic survey tools.
In the Drill Collar article, we have discussed their types, threads, torque and Specifications in more detail.
What is The Drilling Bit?
The Drilling Bit is at the bottom of the drill pipe and is chosen in accordance with the hardness of the formation to be drilled. It can be one of several types. The most common types are roller cone bits and diamond bits. They can range in size from 3¾” to 26” in diameter, but some of the most commonly used sizes are 17½”, 12 ¼”, 7 7/8”, and 6 ¼”.
Roller Cone Bit
Roller cone bits usually have three or four cone-shaped steel noses that are free to turn as the bit rotates with rows of teeth or cutters in each cone. As the bit rotates the teeth in the cone cut or gouge the rock or formation as the cone rolls over it, the teeth may be of made a steel alloy or a tungsten carbide insert fitted to holes machined into the cones.
Most roller bits are “jet bits” with nozzles for the drilling fluid to exit, just like the nozzle on a garden hose. The drilling fluid exits the drill bit through the nozzles at high velocity, striking the bottom of the hole and washing the cuttings away, lifting them out from the bit and up the well bore outside the drill pipe. This action keeps the drill bit clear of cuttings and does not impede the drilling.
You can read the full article on Roller Cone Bit.
PDC & Diamond Bits
Diamond Bits are not of the same structure as roller bits. Instead of roller cones, they are embedded with small industrial diamonds into the sides and bottom of the single fixed head that rotates with the whole drill string. They work using a shearing or slicing motion, unlike the gouging action of the cone bits, and can be used for soft, medium, or hard formations. The only downfall of the diamond bit is the higher cost, but this can be argued against the longer life that it can give, resulting in fewer bit changes.
In the PDC Drill Bits article, we have discussed their components & features in more detail.
Bottom Hole Assembly As A Part Of Drill string:
The Bottom Hole Assembly (BHA) is one of the drill string components that consist of a
- Drilling Bit, which is used to break up the rock formations;
- Drilling Stabilizers, which centralize the drill string in the hole.
- Reamers are used to enlarge the drilled hole for certain reasons.
- Drilling Jars are used to free any stuck pipe that may happen during drilling.
- Shock subs are used to reduce the vertical drill string oscillation (bouncing).
- The hole opener is used to enlarge the hole to a certain size.
- Thrusters
The Bottom Hole Assembly may also contain other components such as a downhole mud motor and rotary steerable system (RSS), measurement while drilling (MWD), and logging while drilling (LWD) tools. The components are joined together using rugged threaded connections. Short “Drilling subs” are used to connect items with dissimilar threads.
Drilling String Design
Ideally, the drill string components should be designed to deliver sufficient weight to the Bit and provide sufficient torsional and tensile strength to withstand vigorous and dynamic drilling conditions. The components should also withstand burst and collapse pressure loads and be designed to minimize hole stability problems. Many factors must be considered in its design, such as:
- Total depth
- Hole size
- Mud weight
- Overpull
- Bottom Hole Assembly Types
- Hole angle
- Pipe weights and grades
- Corrosive environment
- Ability to fishing tools out of hole
If you want more details about the design, you will find it in the DRILL STRING DESIGN Article.
Care Of The Drill String
The previous Topic, “drill string failure“, describes how downhole conditions could damage a drill string. This Topic outlines what can be done on the surface to prevent the expensive loss of time caused by downhole failures. The measures taken fall into two groups:
- Minimizing the damage to the individual items during drill string operations.
- Removing defective items that have not yet failed from the string – in other words, implementing an effective inspection routine.
We define drill string operations as all the incidental activities associated with using the drill string. These activities would normally include:
- During transport: Loading, unloading, and moving the drill string by truck and vessel.
- In the yard: Storing and handling drill string components.
- At the rig: Handling, picking up, hoisting, stabbing, doping, tonging, setting and unsetting drilling slips, drilling, tripping, jarring, jacking, racking, and laying down.
Many of these rig operations involve tools that apply or measure loads to the drill string. Such tools may be pipe handlers, top drives, rotary tables, tongs, torque gauges, slips, pressure gauges, and weight indicators. Proper maintenance, calibration, and operation of these tools are critical for protecting the drill string from damage and keeping applied loads below design limits. The accuracy of the gauges is just as important as knowing the load limits.