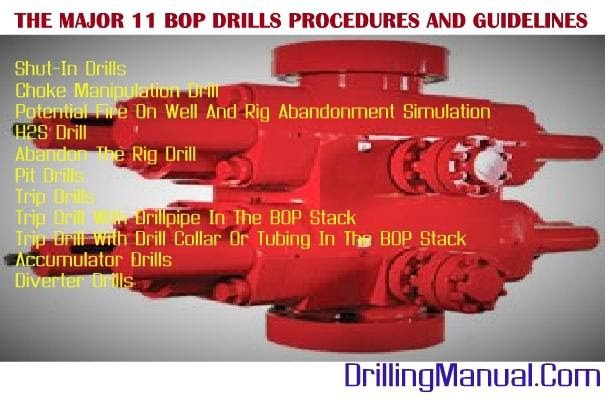
The purpose of these BOP & Well Control drills procedures or exercises is to familiarize rig personnel with the various equipment and with the techniques that will be employed in the event of a Well Kick. Here, we explain all well control drills including trip drill procedure, pit drill in drilling, H2S drill, Emergency drills, and more.
Shut In Drill Procedure
These drills are correct to minimize the time required for the Driller and his crew to shut in the well properly and quickly and to confirm that all essential tools and equipment are available in good operating condition. The Drilling Contractor’s personnel shall conduct drill to close in the BOP, in the shortest possible time, fully comprehending the process procedure.
The recommended procedures:
- Without any previous warning an authorized person should activate the alarm signal to simulate a potential Kick situation ( check also the major Kick warning Signs – Causes of Kick)
- The Drilling Contractor’s crew should follow the established close-in procedure depending on the stage of operations at the current time:
On bottom:
- Pick up the kelly or top drive to the correct height, shut down the pumps.
- Then, carry out a simulated well shut-in.
Well Control or BOP Drill Procedure while tripping Pipe:
Lower the stand into the hole to the correct height and set the pipe in the slips, stab in a full opening safety valve (lower kellycock) in the open position, close the safety valve, the carry out a simulated well shut-in.
To train the rig crews, shut-in well drill should be planned to also cover the following associated operations:
- Pull the Bottom Hole Assembly BHA out of the hole.
- Running casing.
- Wire line surveying.
- Logging (as well for TLC logging, if any).
- Running tubing (single as well as dual completion running).
Choke Manipulation Drill Procedures
The purpose of the ‘choke manipulation drill’, is to provide the drill crews with realistic Well Control training and a feel for the equipment and procedures used for killing a well, by simulating a circulation through the choke manifold under Kick condition.
The choke manipulation drill should be carried out before drilling out shoe tracks.
Drilling Contractor’s crew should run BOP drill procedure and exercise as following:
- Run the Drilling Bit to above the shoe track.
- Break the circulation and record the RPSP.
- Close the BOP Stack.
- Apply pressure to the well and simulate circulation under Kick conditions using the automatic power choke and manual adjustable choke.
- Record the circulating drill pipe pressure and casing pressure.
Consider applying low pressure to the Casing (say 200 psi), and bring the pump up to reduced pump strokes controlling the drill pipe pressure according to a predetermined schedule.
EMERGENCY ‘ON-THE-RIG’ DRILLS
The purpose of these drills is to familiarize rig personnel in reacting to emergency situations that, depending upon their severity ultimately, may lead to the abandonment of the installation.
Potential Fire On Well And Rig Abandonment Simulation Drill Procedures
- Without any previous warning, an authorized person should activate the alarm signal to simulate a fire on the well, followed by rig abandonment. The Drill Bit should be inside the casing shoe and not in a troublesome zone.
- The Drilling Contractor’s crew on duty will Shut in The Well and hang off the drill pipe without opening the hydraulic valve on the choke and kill lines, then continue with the necessary steps to simulate rig abandonment by all unnecessary personnel. In contrast, the emergency crew should simulate the fire-fighting procedure.
H2S Drill Procedures
- Without any previous warning an authorized person should activate the alarm signal, to simulate the presence of H2S. The drill against the H2S effects can be operated at two levels:
- Alarm drills simulate the presence of H2S in the mud.
- Emergency drill simulating the presence of H2S in the air, i.e., in the shale shakers area, on the rig floor, at the mud tanks, etc.
- All personnel except for the crews on duty must wear breathing apparatus. They must proceed to the windward emergency safe breathing area while the emergency crew secures the well and simulates the delimitation of the polluted area.
- H2S drills shall be recorded on the IADC daily drilling report and appropriate company form.
Abandon The Rig Drill Procedures
Without any previous warning an authorized person should activate the alarm signal, to abandon the rig due to a potential uncontrollable fire on board, uncontrollable blow-out situation or damage to rig structure etc.
All Personnel except the crews on duty must get ready to abandon the rig. Operations must be suspended for the time the drill is carried out.
Well Control Drills
The severity of any well Kick can be reduced if it is detected early enough. Crews must be able to recognize the indications of a potential kick and be able to close in the well properly in the minimum possible time. These drills are intended to test the driller and mud logger (Mud logger Job Description) on their alertness with regard to an increase in pit volume and to verify that pit level equipment and indicators are operating correctly.
The Company Completion & Drilling Supervisor shall plan the drills and evaluate the performance of the rig crew.
No advance notice shall be given that a drill is to be conducted, in order to test the degree of vigilance being exercised by the driller and the mud-logger.
The time from the moment the drill is initiated, until the crew has reacted to shall be recorded, along with the total time needed to complete the drill procedure by closing BOP. All drills and responses shall be recorded on Company Daily Drilling Report and IADC Report. Pit drills shall be recorded on the Company’s appropriate form.
To complete the drill, The Drilling Contractor’s crew should also fill in the Kill Sheet. SIDPP and SICP values will be provided by the Company Drilling rig supervisor and Completion Supervisor.
Pit Drills Procedures
The purpose of this drill is to ensure that the drill crews are familiar with the Soft / Hard Shut In Procedure implemented in the event of taking a Kick While Drilling. These drills can be conducted in either, cased or open hole. However, if the Drill String is in open hole, the well will not be shut-in.
- Without any previous warning an Authorized Person, will change the pit level indicator, to show an increase in mud volume.
- The mud logger is expected to detect the gain and notify the Driller. The Driller is expected to perform the following:
- Detect the pit gain.
- Pick up the kelly or top drive to the correct height.
- Shut down the pumps and check the well is flowing.
- Shut In the well as per the established ‘Soft / Hard Shut In Procedures’: open the hydraulic valve on the BOP stack, close the upper bag-type preventer and close the remote choke.
Trip Drill Procedure
The purpose of the trip drill procedure is to ensure that the drill crew is familiar with the Hard /Soft Shut In procedure to be implemented as described above. The drill shall be performed with Drill Bit inside the casing setting depth and not in a troublesome zone.
On floating rigs, the trip drill should include the procedures for hanging the string on the BOP stack as per normal practice.
- An Authorised Person (without any previous warning), will initiate the drill by manipulating the trip tank indicator or flowline indicator.
- The mud logger shall detect the gain or incorrect pipe displacement and notify the Driller.
Trip Drill Procedure With Drill pipe In The BOP Stack.
The Driller is expected to perform the following:
- Detect the pit gain or incorrect pipe displacement.
- Lower the stand into the hole and set the pipe in the slips.
- Install a safety valve (lower kellycock) in the open position.
- Close the safety valve.
- Check for well flow.
- Shut In the well as per the established ‘Soft / Hard Shut In Procedures’: open the hydraulic valve on the BOP stack, close the upper bag-type preventer and close the remote choke.
- Install Gray valve IBOP.
- Open safety valve and prepare to strip in hole with Drill Pipe.
Trip Drill Procedure With Drill Collar Or Tubing In The BOP Stack.
The driller is expected to perform the following:
- Detect the pit gain or incorrect pipe displacement.
- Lower the Drill String tool joint or drill collar connection to a working height (it may be necessary to install and run a stand of Drill Pipe or tubing to allow closure of the BOP).
- Set the slips, ensure that no stabilizer or other non slick tool is across the preventer.
- Install the safety valve (lower kellycock with a crossover) in the open position.
- Close the safety valve.
- Latch onto, pick up the pipe, remove the slips and check for well flow.
- Shut In the well as per the established ‘Soft / Hard Shut In Procedures’, open the hydraulic valve on the BOP stack, close the upper bag-type preventer and close the remote choke.
- Install a Gray valve IBOP.
- Open the safety valve and prepare to perform stripping operation in to hole with Drill Pipe.
BOP Accumulator Drills Procedure For Well Control
The purpose of this drill is to minimize the cause of equipment failures, to ensure quick initial closure times, and to check the ability to continue operations in the event of BOP accumulator pump failure. Accumulator performance shall be proven at the first installation of the BOP on the wellhead. Thereafter, this drill should be conducted after each Casing setting before the BOP pressure tests.
The following well control drills procedure is recommended :
- Position a joint of drill pipe (API Drill Pipe Specs) in the stack. Make sure the tool joint is not access the BOP rams.
- Turn off the accumulator pumps.
- Record the initial accumulator pressure. This pressure should be the design operating pressure of the accumulator. Adjust the regulator to provide 1,500 psi operating pressure to the annular preventer.
- Close then open the annular preventer, hydraulic valves on choke and kill lines and the pipe ram preventers for the size of the pipe being run. Closing times shall be less than 30 sec for each ram-type preventer. Closing time should not exceed 30 sec for annular preventers smaller than 18 3/4” nominal bore and 45 sec for annular preventers of 18 3/4” and larger.
- Record the final accumulator pressure. The final accumulator pressure shall not be less than 1,200 psi (84 kg/cm2).
- Bleed the accumulator pressure down to 1,000psi (precharge pressure). Turn on the accumulator pumps and record the recharge time. The recharging time from 1,000 psi to 3,000 psi shall be less than 15 min.
- Reposition all the preventer control valves in the normal operating mode.
Equipment that does not meet these requirements, either, has insufficient capacity or is not in good operating condition and needs repair. At the end of this BOP drill procedure, a function test will be conducted to run the accumulator electric pump using the rig emergency generator. Also, you can perform all BOP Control System Tests from time to time to ensure everything is going ok.
Diverter Drills Procedures in Well Control
Because of the limited response time required when diverter systems are employed, the Drilling Contractor shall have written procedures that detail specific emergency action plans. These emergency action procedures should be in operation prior to spudding the well.
The purpose of diverter drills is to reduce to the minimum, the time required for a driller and his crew to divert the well flow during a Kick. Diverter drills shall not be limited to the rig floor personnel but shall involve all rig personnel. The drills will be prepared in line with the specific procedure that will be adopted in the event of a shallow gas kick.
This well control drill shall be conducted hourly with each crew until the crew is familiar with the drill.
The Driller is expected to perform the following:
- Pick up the kelly or top drive so that lower kellycock is above the rotary table.
- Open the diverter lines, close the diverter element and close the shaker valve (auto sequenced operation). Check the closing time (for diverter sizes smaller than 20” the closing time shall be within 30 sec, for diverter sizes 20” or larger the closing time should be within 45 sec).
- Circulate through both lines.
Drills Frequency & Response Times
Training Period
- Shut-in drills.
- H2S drills.
These tests shall be carried out on each shift basis, at the beginning of any new activity, any time experienced personnel are replaced with new recruits, especially when key position personnel is involved such as the Toolpusher, Driller, and Assistant Driller. Well Control drills shall be repeated until every crew member gains the correct experience and training.
- Choke manipulation drill. This drill should be carried out prior to drilling out surface or intermediate casings string.
Routine Drills
- These well control drills shall be executed every week. Potential fire on wellsite and/or abandon rig.
- Alert or emergency drills have to be performed weekly and repeated before entering the zone where the presence of H2S is suspected, before coring and before making DST or a production test when the presence of H2S is, either, predicted or ascertained.
Well Control & BOP Drill exercise:
- Pit/trip drills shall be carried out on a shift basis every fortnight. These drills shall be conducted also when the well is nearing or entering high-pressure zones.
- Diverter drills shall be performed prior to drilling out the conductor casing string.
Timing
Time is the most important aspect in shut-in drills and pit drills, and the times required to accomplish the given task shall be recorded.
The well control drills Reaction times that can be considered as satisfactory to accomplish different drill requirements are detailed below:
- Shut In drills. One minute from activation of the alarm signal to being ready to close the bag-type preventer.
- Pit drills. Not more than 2.5 min from an observable change in drilling fluid volume to the time the well is closed-in, implementing the soft shut-in procedure.
The correct timing for all other tests will be defined in the Drilling Contractor’s Procedures according to the equipment characteristics.