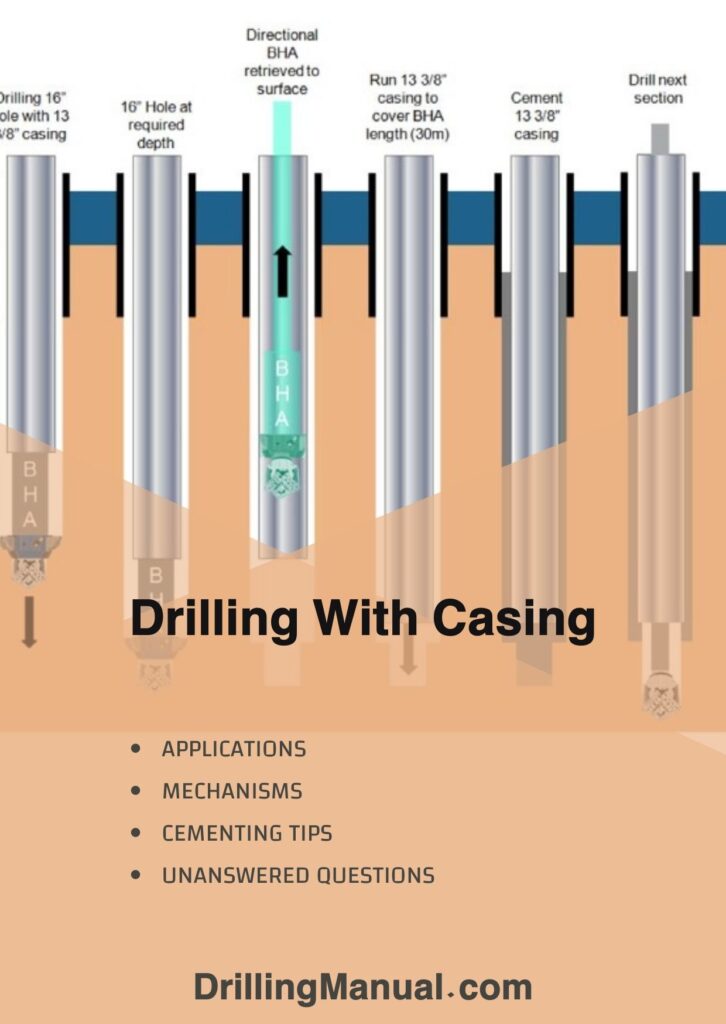
Drilling with Any of the casing types & casing liners is not new. It was routine practice in some shallow fields between 50 and 60 years ago to attach a drilling bit to a small-diameter production string, drill a few hundred feet, and leave it on the bottom once total depth was reached. Outside that limited sphere, it was generally recognized that conventional drilling would have some obvious advantages if casing could be used as a drill string without making a tripping pipe. The earliest general thinking was that the ability to drill with casing would:
- Reduce or eliminate trip time.
- Eliminate the need for a separate drill string.
The big drawback to the whole idea was that bits did not last very long. Unless there was some dramatic improvement in bit life (bit dull grading) or some way to retrieve and replace the bit without tripping the casing, there was no reason to consider the process except in the limited context of shallow wells. In recent years, technological improvements along those lines and the development of rigs specifically built for drilling with casing brought about a considerable change. As a result, the two benefits have begun to be realized, but so too have many other benefits that are in the details of the process. Some are obvious, some are not. Before compiling a list, it might be best to describe the process so that the advantages become more apparent.
Drilling Methods & Mechanisms With Casing
Some of the shallow wells drilled with casing in northern Louisiana in the 1940s and early 1950s were drilled “on the cheap,” so to speak. Typically, a reconditioned bit was welded to the pin end of a 4½ in. casing joint, and the well was drilled to a depth of a few hundred feet. The drill string/casing string consisted of about 15–20 pipe joints and was cemented (Casing Running Checklist – Casing cementing procedures) as soon as the total depth was reached. The bit was left on the bottom of the string. It was a crude process based almost entirely on its economic advantage.
The current processes of drilling with casing are considerably more advanced. There essentially are four approaches:
- First, rotation drilling with conventional bits.
- Second, rotation drilling with expendable drill-through bits.
- Third, rotation drilling with wireline retrievable bits.
- Fourth, Slide drilling (with or without rotation) using retrievable downhole motors and bits.
The rotation drilling with conventional bits.
The first case essentially is the same technique as the early methods, except the technology is several orders of magnitude more advanced. However, the general concept is the same in that the bit is a permanent part of the casing string, and if it fails before the total depth is reached, then the casing must be tripped to replace it. This method is typically used for a final production string of casing or a final production liner (liner hanger system). Subsequent deepening of a well drilled with this procedure requires a window or section milling operation and a well sidetrack. However, this method is unlikely to be used if deepening is a consideration.3
Rotation drilling with expendable drill-through bits
The second method differs slightly from the first in that the bit does not form a permanent barrier on the bottom of the casing string. The bit is designed to be drilled through with another bit that will pass through the casing. These expendable bits are drag-type bits with PDC cutters set in a drillable matrix material (PDC Drilling Bits Guide). This method also has a particular disadvantage in common with the first method, in that if the bit fails before the required depth is reached, then the casing must be tripped to replace it. Typically, this method is used for surface casing strings or relatively short sections, where bit life is not a significant factor.
Rotation drilling with wireline retrievable bits
The third method is the heart of the new technology and the true significant step that makes the drilling with casing process truly viable as an alternative to conventional drilling. Current tools allow the bit to be retrieved and replaced by wireline so that dull bits may be replaced with new or different types of bits. It is possible to keep the casing in motion during the retrieval and replacement process to prevent pipe sticking, if that is a potential problem.
Slide drilling (with or without rotation) using retrievable downhole motors and bits
The fourth method of using retrievable down-hole motors has been used primarily in drilling with liners but also is the method by which directional wells may be drilled with casing. With this method, both the motor and the bit (as well as directional tools) may be retrieved and replaced using a wireline.
The methods just described have several variations, but that is the essence. These methods are necessarily accomplished with a top drive system rig, although the drilling with a liner could be done with a conventional rotary rig. The best results are with rigs specifically designed and built for drilling with casing. Many of these rigs already exist, and more are likely to be built as the process gains wider acceptance. In addition to conventional and special bits for these applications, special under reamers (Reamers Types) have been developed for drilling below a cemented casing string to provide more clearance while drilling and for cementing in drilling.
Casing Design As a Drill String
The casing used in drilling obviously undergoes stresses not normally considered in conventional casing design. Primarily, the difference is in the addition of torsion-induced shear stress. While it is common practice to rotate liners while cementing, it is not that common to rotate full casing strings because of the high torque required to do so. The torque (Torque and drag in drilling) required to rotate most full casing strings exceeds the maximum recommended makeup torque of the connections, so torsional stress in the casing body itself is seldom even considered.
Casing Connections
When the casing is rotated for drilling, the casing connections are first considered. Casing connections are usually thought of as one-time makeup and are never intended to be tripped in and out of a wellbore. Anyone who ever had to pull a full casing string out of a well can attest to this. Standard API 8-rd threads are especially bad because a good percentage of them gall in such a process. This is true of many interference types of threads in general, but any type of thread that is not properly lubricated with approved thread lubricant can experience galling problems.
The basic premise for drilling with casing is that the casing will not be tripped, but in reality, a trip always remains a possibility, even though it is remote. The main concern with many types of casing connections is the possibility of over-torquing them to the extent of causing damage. This is especially significant in connections that do not have a shoulder. So the main concern with torque for most drilling with casing applications is not damaging the connections.
One solution is to use only shouldered connections. This can be a rather expensive solution. Another possibility that has proven effective is the use of stop rings, in other words, inserts in the couplings that allow the pins to make up into the coupling to a specified depth and no farther. This represents a sound, inexpensive alternative to shouldered connections. While such rings have been used in ST&C and LT&C 8-rd connections for some casing rotation applications, these connections are not considered good choices for drilling with the casing. For drilling applications, buttress threads with stop rings have proven a much better choice.
Body Strength
We discussed the effects of combined loading in previous articles (casing Loads design). The only thing to add as far as drilling is concerned is torsion. So, by knowing the internal and external pressures and axial load, we can calculate the radial, tangential, and axial stress components, just as we did in the previous article. We also considered axial stresses due to bending in curved wellbores and gave the formula for calculating the additional shear stress component due to torsion. All those stress component values are substituted into the von Mises yield formula to determine the combined load, which we compare to the yield strength of the casing. In most cases, a string adequate for the normal application as casing should also be adequate for drilling as far as the casing body goes.
However, one additional aspect of casing design that is unique to drilling with casing is the matter of casing collapse. One normally would consider that collapse occurs only near the bottom of a casing string, but that may not always be the case when the string is also used for drilling. Suppose that, while drilling a well with casing, we experience a gas kick.
How do we kill the kick? (driller’s method – wait and weight method) We do it the same way we do it with drill pipe: We mix a kill-weight mud and circulate the gas bubble out, holding enough back pressure on the choke (choke manifold) to keep the annular bottom-hole pressure slightly above the formation pressure. No problem there because that is fairly routine.
But what do we normally do when we get the kill-weight mud to the bottom of the drill string? We normally stop the pump to ensure the surface drill string pressure reaches zero. This is how we check whether the “kill-weight” mud is actually “kill weight” and whether the kill sheet calculations are good; it is our first and best opportunity to check this.
Now consider that our drill string is casing instead of drill pipe, so the internal-volume to annular-volume ratio is quite different than in a conventional scenario. In this case, we likely already have gas to the surface when kill-weight mud is at the bottom of the casing string. Think about the surface pressures. The pressure on the inside of the drill string/casing string is effectively zero, and the annular pressure is the confined gas pressure at the surface. The casing at the surface also has the maximum tensile load of the entire string at that time. Is the combined casing tension and collapse strength of the casing string sufficient in this case?
This is something that should be considered in our casing design. We are not accustomed to thinking in terms of casing collapse at the surface in a situation such as this, but this is something we must consider now because such a casing collapse could be disastrous. We likely have a “wet buckle”; in that event, we can no longer circulate the well from the bottom.
In some oilfield companies, we considered that there is a gas kick while drilling below the 9⅝ in. intermediate casing. This is a rather extreme example of a gas kick that fills the entire annulus, which we would like to think would not happen. Whether we could have such an event is debatable, but it represents a worst-case scenario. This is something that should at least be considered in our casing design if the casing is also going to serve as a drill string because we are not accustomed to considering collapse in casing design anywhere except near the bottom.
Casing Wear and Fatigue While Drilling
Casing wear is always considered from the inside as opposed to the outside. The rotation of a casing string while drilling will obviously cause some wear on the outside of the string. We could use techniques like calculating the contact force to determine where the wear will be the most significant, and that should prove reliable, just as before, but the difference is that, in this case, the casing string is not static.
Such a method would tell us at what depths in the borehole the wear will be greatest, but it will not tell us where in the casing string the wear will be the greatest because it is not static concerning the borehole. We probably could develop some rotation time and contact force correlations, but that would require data we may or may not have. Certainly, this can be developed in the future, but the assumption is that any casing in the open hole is subject to wear and must be protected. Currently, this is accomplished with wear rings that are crimped onto the casing with hydraulic tools specifically designed for that purpose. Practical experience so far shows that this is effective.
Fatigue of casing in drilling operations has certainly not received the amount of study that the drill pipe has. The principles essentially are the same, except for the different types of connections. Casing fatigue as related to drilling string harmonics has been observed in practice. Wellbore curvature in directional applications might cause some fatigue problems, too, although that has not been seen in practice so far. Increasing applications of drilling with casing will lead to further developments in this area.
Cementing in Casing While Drilling
Cementing a casing string that has been used to drill the borehole in that hole should be relatively easy. Special float equipment has been developed to use while drilling or to be inserted into the string once drilling has been completed. The casing string can be reciprocated and rotated during cementing to aid in the displacement of the mud, which is generally not possible in conventional cementing operations. Crimped-on casing centralizers have been developed and are run with the casing initially.
These are rigid with curved blades to aid in mud displacement. It appears the only things that cannot be run are sidewall scrapers and wipers. With good-quality mud, centralizers, and pipe movement by reciprocation and rotation, adequate mud displacement should not be a problem in cementing. Liners used as drilling strings may be cemented similarly. Liner hangers have been developed so that the liner may be hung and cemented immediately after drilling.
Advantages
Having discussed the casing and liner drilling operations, it seems that a list of advantages is now in order, and most of these should already be obvious:
- Trip related
- Time savings.
- No drill collar handling.
- Less wear on equipment.
- Lower chance of swabbing.
- There is less chance of surge fracturing formations.
- Crew related
- Less crew exposure to pickup and lay-down operations.
- No derrick man for numerous trips.
- And no casing crews.
- No casing elevator or stabbing board with which to contend.
- Drilling related
- Lower circulating rates and pressures.
- Better cuttings transport (reduced annular volume).
- Better control of equivalent circulating density.
- Overall better well control while drilling.
- Less chance of differential sticking in most cases due to pipe movement.
One other interesting phenomenon observed in some actual drilling cases is a reduced tendency for lost circulation where it has been a known problem in the same area with conventional drilling. This has been attributed to the formation of filter cake or compaction of mud filter cake into formation pore spaces at the bore-hole wall. A filter cake or plugged pore spaces cannot make a formation stronger per se, but as discussed before, the fracture pressure of a formation is lower if the fracturing fluid can enter the pore spaces prior to fracture. It appears that what has been observed in these cases is that the drilling fluid is unable to enter the pore spaces prior to fracture.
While it is possible that the rotating casing more thoroughly “packs” the pores on the formation face with mud filter cake, it also opens the question as to how much damage is done to the filter cake in tripping the drill pipe. It is also possible that the effect of the trip surges on the formation is not always apparent during the trip itself. This remains an interesting phenomenon for further investigation.
Unanswered Questions
Despite the advantages of drilling with casing and liners, obviously, questions remain unanswered or only partially answered. They are related mostly to equipment development, reliability, availability, and so forth; and there are questions regarding specific issues such as
- Fatigue failures of casing.
- Actual casing wear.
- Cementing reliability.
- Differential sticking tendencies of larger-diameter pipe.
- Consequences of trips with casing if the necessity should arise.
These are questions that will be answered in time and as technology develops. It should be apparent from this discussion that we have not examined the economic benefits of drilling with casing or liners, and that is not a subject for this particular book. A fair portion of what has been done so far has been experimental and developmental in nature. However, definite economic benefits are being demonstrated in certain locales, and there is no reason to think that they are limited to any particular area. Those benefits must be evaluated on an individual basis.
I suggest for you this great paper “Successful Use of Directional Casing While Drilling” to download and read from the below link
References:
- Casing & Liners For Drilling & Completion